I have been looking for a small form factor oscilloscope for a while to use as a spare oscilloscope and to bring along to customers. I could have gotten a Rigol 1000Z or something like that but I wanted something which packed a bigger punch. I had spotted a Yokogawa DL1740 (4 channels 500MHz) with two defective channels (1 and 4) on Ebay but as usual the seller wanted too much money. A couple of weeks of patience paid off because he dropped the price down to $300 and decided to put it up for auction. At that point I decided to take a stab at it even though the price was still too high but sometimes it happens an item sells for more than the previous price after a price drop.
The reason I picked this oscilloscope is because it also has the LAN connection option, reasonable long memory (up to 1Mpts), a color TFT screen and PC software which is still being maintained by Yokogawa (the latest version is only a few months old). This oscilloscope also has some nifty features like sending a screendump to an FTP server after each trigger and/or sending an e-mail. I get the impression that the oscilloscopes from Yokogawa are also geared towards long term monitoring of signals.
When I unpacked it I was surprised to find it also has a pouch for probes and maybe a mains lead. Some photos of the case:
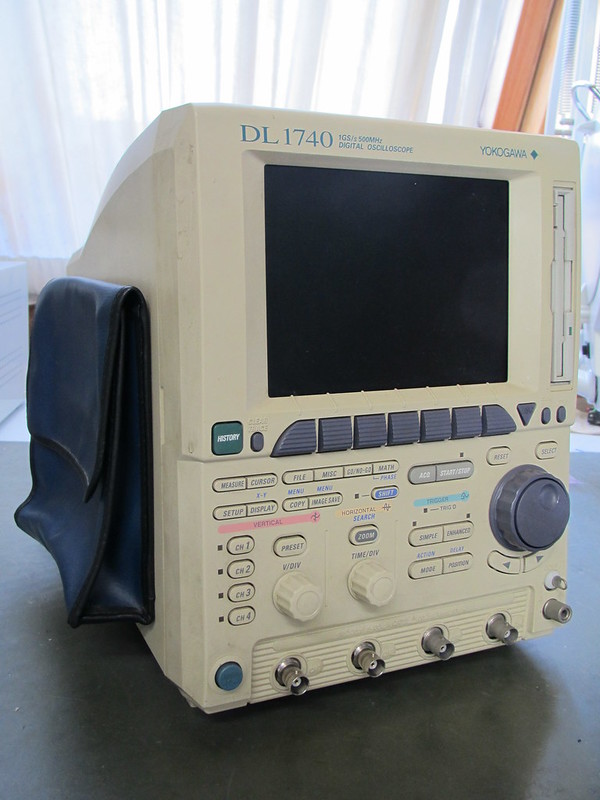
The oscilloscope says 1Gs/s on the front but that is only in half channel mode where channel 1 & 3 use two (interleaved) ADC converters. However, it can also do equivalent time sampling so it is not entirely useless for measuring 500MHz signals. Oh... and how cute is that pouch on the side? I think I'll nickname it Aussie...

It is almost typical for Japanese equipment to get so discoloured over the years. The contrast between the disk drive and the case makes it painfully visible. The blue parts turned into some teint of purple.
It does have this nasty error message due to two channels not working:

Time to take it apart. Fortunately I managed to buy a service manual for this oscilloscope from Ebay for a few euro. That has a block diagram of the circuitry (of course no schematics) and the way to take it apart which isn't straight forward with a compact unit like this oscilloscope.
The front:

CPU board (note the buzzer glued to the large chip in the middle!):

The CPU board has an ethernet daughterboard attached to it. Judging from the amount of memory I guess the ethernet board does all the heavy network lifting by itself. The extra slot is for a SCSI + serial port interface option I don't have. The SCSI interface allows to connect an externel SCSI hard drive for storage. At the bottom right there is a connector for a floppy drive or a ZIP drive. I have not investigated the ZIP drive connector in much detail but it may be an IDE/PATA compatible interface. From the traces on the CPU board it may be connected to the data bus.
I wanted to push on to the pressing matter of the two channels not working so I focussed on the acquisition system. The acquisition system consists of two board piggy backed together. On the opposite side of the acquisition board is the digital data handling & storage board:

This is where the data from the ADCs is stored into SRAM (left part of the board). The signal post processing happens on the right side of this board. The DRAM is used to store previous acquisitions. This oscilloscope does not use segmented memory (it could have) but uses extra memory to store previous acquisition which can be recalled using a history button. Last but not least the section which drive the display is also on this board which is why the VGA output connector is also on this board.
The acquisition board:

The 4 ADCs in large QFP packages are easy to spot on the right. The smaller chips are the trigger comparators. Fortunately the attenuator and pre-amplifiers are in two seperate modules providing two channels each. Swapping the attenuator/pre-amplifier modules quickly showed that the primary problem is not in the main board but in the modules. The ADCs all work and offset controls also work. Because the calibration is off it is hard to determine what is causing which problem. With the modules swapped is was very hard to make the oscilloscope trigger so I decided to dig deeper into the acquisition board to make sure it worked OK. One thing I was missing where DACs to make the various DC control voltages. It turns out the big QFP chip in the middle is generating PWM signals which are then filtered using RC filters and made bipolar using opamps. One of the interesting discoveries I made has to do with the offset. The oscilloscope has two signal offset controls. One adjusts the offset in screen divisions and the other in Volts. Both offsets adjust the same control voltage!

Anyway, when I swapped the modules back to their original position triggering worked again.
The attenuator/pre-amplifier module front and rear:


Besides the relays there are three chips. The one in the middle is a mux which switched between normal and interleaved mode. The pre-amplifiers are under a lump of heat conductive silicone rubber. The pre-amplifier chips do a lot: amplify the signal, bandwidth filtering, prepare the trigger signal + offset, apply DC offset and output a differential signal towards the mux. Yes they get very hot! After some probing and testing it turns out two channels not working is caused by the pre-amplifier chips. Bummer because they are made by Yokogawa. Oh crap

Sitrap: I have two working channels, one is flaky (unstable) and one is not working at all.
OK. A two channel 500MHz scope for $400 ($300 + $100 for shipping) ain't bad but it would be nice if I could make channel 1 & 3 work so I could use the interleave mode. So I decided to get my hot-air station and swap the pre-amplifier chips. I decided to leave the completely dead one out (less heat) but keep the flaky one just in case it could be useful.
More bad news:

It turns out I'm not the first one swapping these chips! The signs of a replacing a chip gone wrong. This damage typically comes from whiping the pads with solder wick. I used to do that too but I found out it is much better not to try and remove the old solder. Instead I remove any flux residues using ethanol or flux-off, apply fresh flux and just reflow the chip in place. After that some touching up is enough to make it perfect.
I think one of the root causes is that the attenuator/pre-amplifier modules get no airflow at all so I'll drill some holes in the plastic outer shell to leave air in at the attenuator/ pre-amplifier modules. I did manage to track down a Chinese chip broker who claims to have the pre-amplifier chips for sale. Their price is reasonable so I'm going to try and order 4. Knock on wood! One of the less pleasant things about the DL1740 is the noise from the fan. It's not very quiet and it doesn't have much openings to let air in (two to be precise: at the top where the printer is and at the bottom where the ADCs are) so the fan is not moving much air.
On to playing a bit with my 'new' scope...
One of the things I wanted to try is FTP access. Setting up an IP worked after a reboot of the scope. After that I can access the floppy drive from my browser and download images. Added bonus: I now have a network attached disk drive so I can read disks from my PC again!


From the last picture it seems it also has some form of intensity grading. So far most of the operations have been straightforward (didn't need the manual) but there are some differences. Japanese oscilloscope makers have a habit of calling peak-detect 'envelope mode' and on the DL1740 you won't find an FFT math operation. It is called PS (power spectrum) instead.
edit: typos