The rectangular cut-out for the display is done extremely well, wonder how it was made. (SNIP) The counter does work (at least in the 50 MHz mode). But this one's really meant as a parts mule.
I would assume it was stamped.
I thought of that, but hobbyists usually don't have that equipment. Reading all the 'Electronics World' from the fifties and sixties I understand that it was not so rare then to build your chassis yourself, and there were also ads for 'Greenlee punches' (I assume we mean the same thing). They are perfect for tube sockets or D shaped holes. But this size?
-group-therapy-thread/?action=dlattach;attach=778062;image)
I've made a great many such panels using just these tools; like with anything worth doing, prep makes all the difference. You start by laying it out with a good rule, Sharpie and a scribe to get perfect lines. You COULD use Dy-Kem Blue if you happen to dabble in lathe work, but Sharpie is a lot cheaper.

Then you make a ~10mm hole close to each corner, and start nibbling. There ARE electric-powered equivalents to these, but for precise openings they just don't offer enough control. First you nibble the corners square, then start nibbling around the perimeter right next to, but NOT on the scribed line. The closer you get, the less file work you'll have later. Cut as much as you can from the BACK of the work for the cleanest lines; but sometimes you just HAVE TO cut from the front. Make allowances for this when laying out.
The file work is where patience really pays off. you'll use a 12-16" (size of work surface) single-cut mill (type with smooth diagonal cutting edges) bastard (fineness of cut between COARSE and 2nd CUT) file. For big jaggies you'll knock the high points down by push or pull filing towards the BACK of the work. This makes all your burr edges manifest on the back edge. Pull-filing helps to mitigate the file snagging on edges and "hopping" which can scar up the work edges, or worse, the face of the panel. You want to clamp the metal so the vise is as close to the surface you are cutting as possible; this eliminates flex-induced movement of the work that will also cause "hopping".
You may need a smaller file to do the vertical edges of the opening that tend to be much shorter; you need a file 1/3 to 1/2 the width of the edge or so to have room for draw-filing later. In some cases, a square or triangle file is your best choice; as long as it is a single-cut file of reasonably fine pitch, you can interchange them for this work. Just remember that the wider your file's cutting surface, while still allowing room to work, the better the smoothing effect of later draw-filing.
Once you have the edges of the opening within 0.20-0.30mm or so of the scribe line all around, you'll switch to draw-filing to square everything up perfectly. This is done by holding the file perpendicular to the work, and pulling the file from side-to-side. This technique leverages the angled cutting edges to makes a much finer cut that tends to "average-out" the depth of cut across the entire stroke. This is how you make the slightly jagged edges from the nibbler (these will become much less pronounced as you hone your technique) perfectly smooth. The scribe lines show you where you need to concentrate your work to bring everything perfectly square.
Remember to stop and "card" your file frequently with a wire-brush or file card; this keeps it cutting smooth & clean.

After the opening is perfectly square, you'll switch to either a finish-cut file or sandpaper on a block or emery boards to deburr; your burrs should be very thin and easily smoothed-out, or often are perfectly fine to ignore, thanks to the smoothing effect of draw-filing.

After that, you flatten out the face of the panel by orbital sanding with a sanding block, or if the piece is small enough, by gluing a full sheet of 220-500 grit to a glass or acrylic sheet and smoothing with an orbital motion prior to priming & painting. Care painting around the edges of the opening really pays off; an even, slightly heavy coating will hide any remaining imperfections.
This video is a good quick & clear primer on files & how to choose & care for them.

mnem
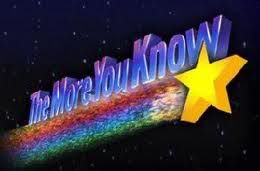