I guess this is more of a repair process than a full on teardown, but I did take the lid off, so anyway.
I got hold of a lovely Fluke 8840A off of Ebay a couple of weeks ago.
I received it in good time and upon powering it up it appears to work correctly and was as accurate as I could tell. The VFD was a bit dim, but I put this down to the age of the instrument.
Alas, after about an hour, it suddenly shut down. The outer casing was also unreasonably hot. Closer inspection revealed that the mains fuse was open, but also more importantly, it was four times the correct rating. The correct fuse for 240v operation is 0.125A.
I took it apart and referred to the circuit diagram included in the user manual (they just don't include that sort of thing in user manuals these days). The circuit diagram of the power supply section even states how many ohms to expect on each winding of the transformer. The transformer in this instrument measured close to shorted turns and most of the rest read a lot lower than stated.
So, having concluded that the transformer is dead, I contacted the seller who was willing to replace the unit and reimburse my return postage, which jolly kind of them.
However, after giving it much thought, I decided I wanted to keep this particular meter because it was fully loaded with the AC option board and the IEEE option board. I had also seen some smashed 8840A's going for a fair bit more than what I had paid for mine, so I decided that I'd be better off winding my own replacement transformer. The original transformer is fully encapsulated making it very difficult to re-wind.
I selected a toroid transformer with two secondaries of the correct voltage for some of the windings required and then I'd wind the rest of them myself. Toroid transformers are relatively easy to wind at home without any special tools.
Right, so, let's get set to work.
Here is the original transformer. I wouldn't fancy re-winding that. I can be done, but it's a proper mission.
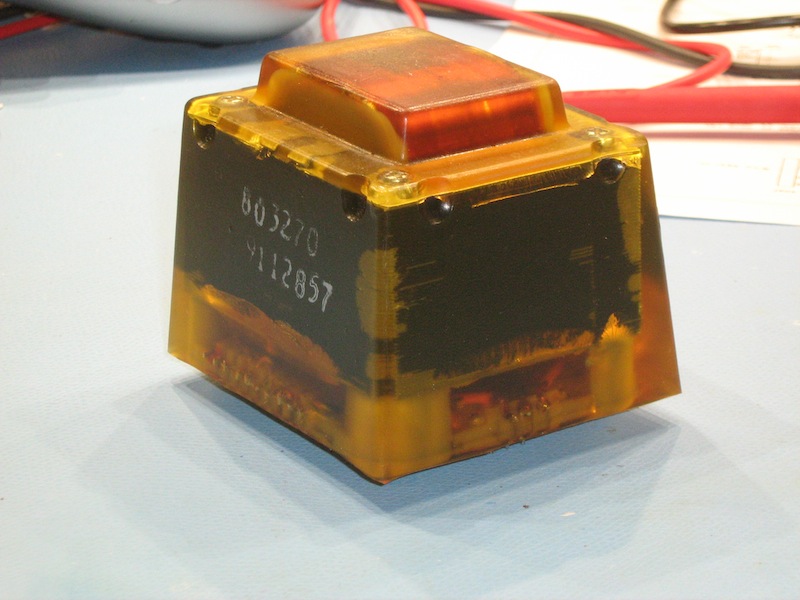
Here is the meter with the transformer removed. I also took the opportunity to re-cap it. There are only six electrolytics in the whole thing, so considering the age of the instrument and the recent extreme heat cycles it my have been subjected to, replacing these capacitors seemed sensible to me.
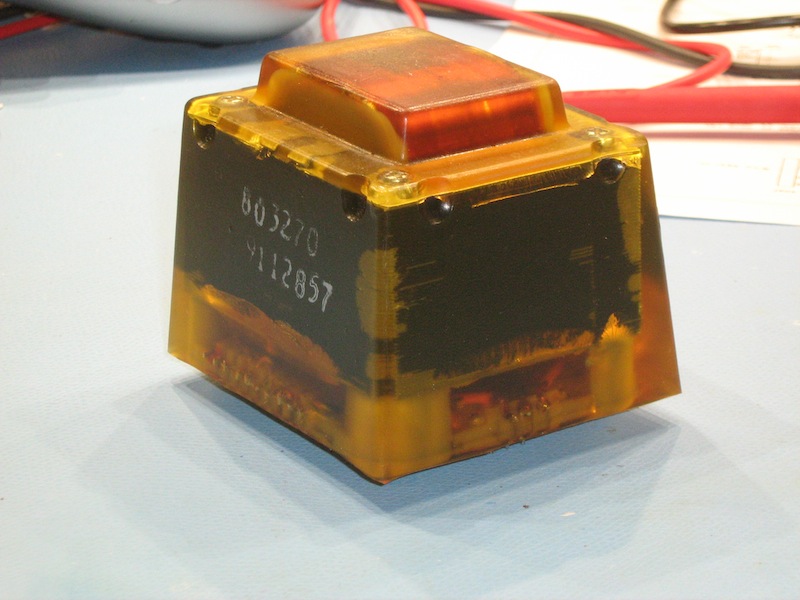
This is the toroid transformer that I got hold of. Here I am measuring the volts per turn so that I can calculate how many turns I need each of the additional secondary windings to be.
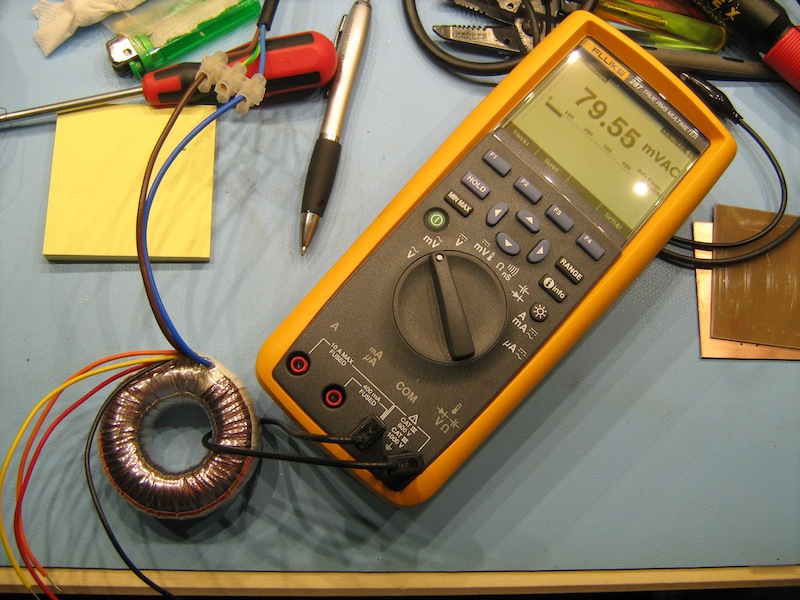
I have got some turns wound using my special stick with a measured length pair of secondaries wound up and down it. The stick threads the wire through the hole in the middle of the transformer rather like the shuttle on a weaving loom.
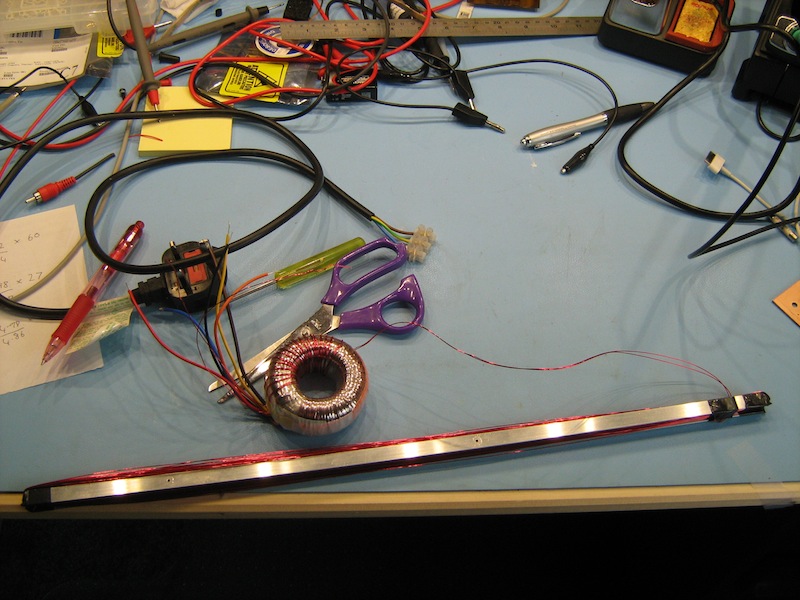
One pair of secondaries wound.
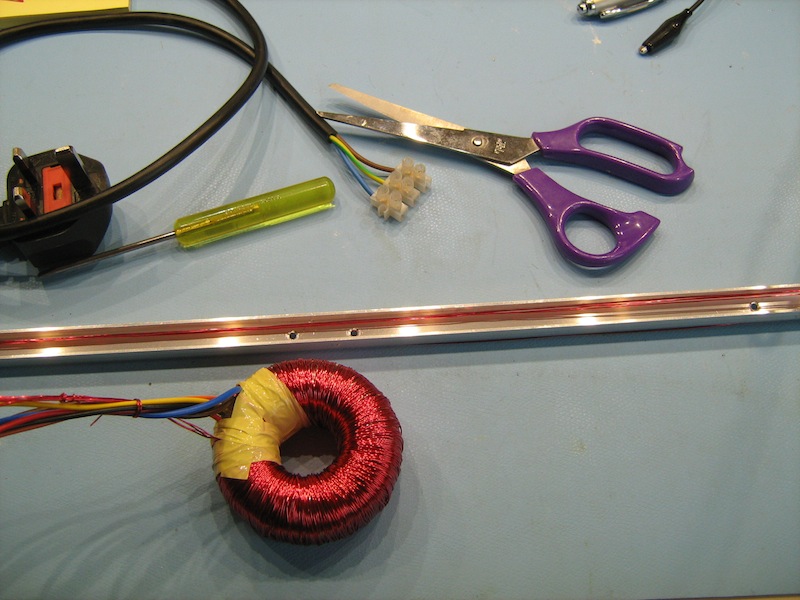
All of the secondaries wound and undergoing testing.
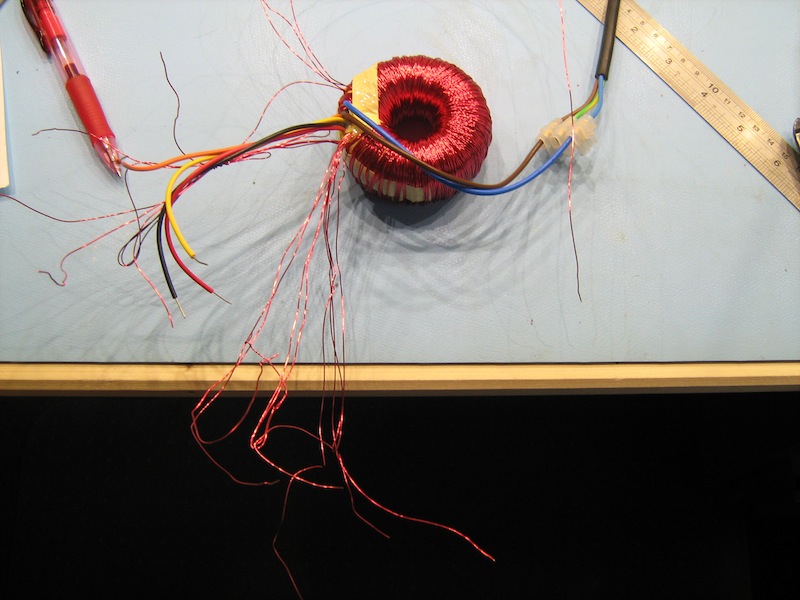
Now all of the additional windings need to be trimmed and terminated into flexible leads.
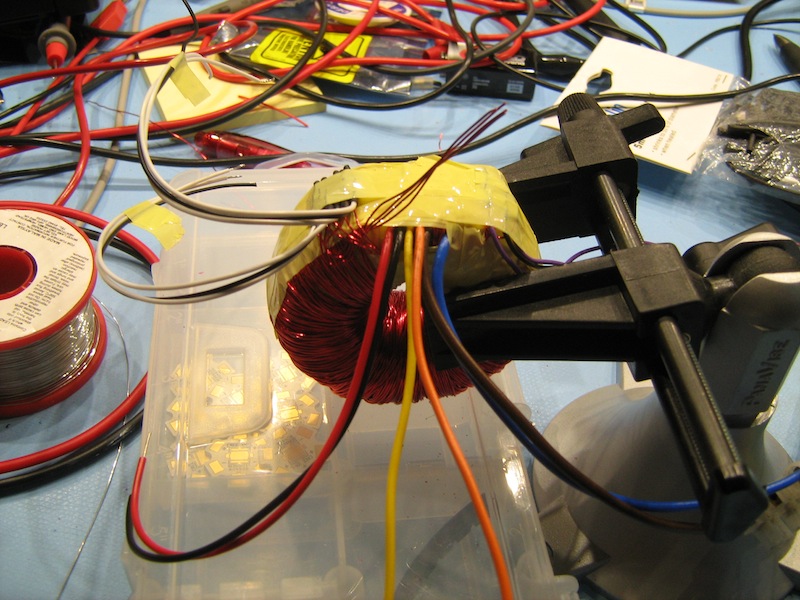
Then, it's all wrapped up in Polyester tape.
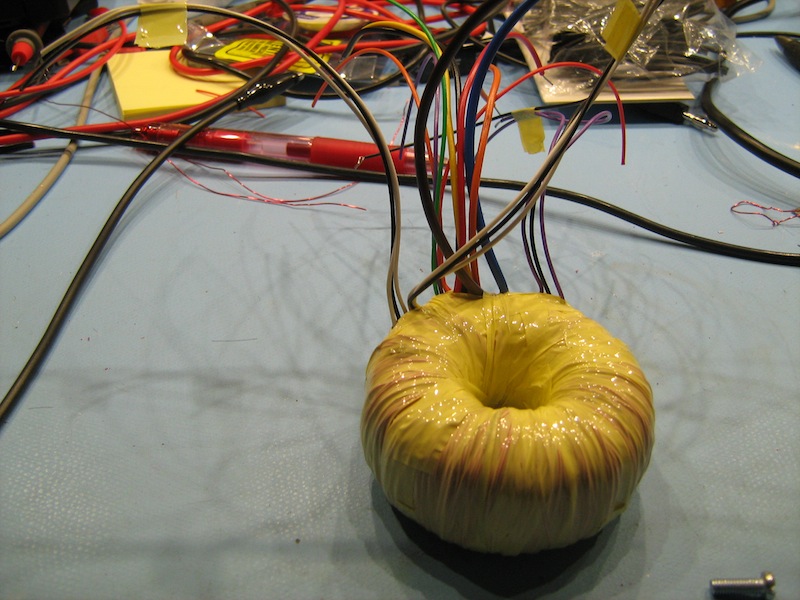
After a final test, all the secondaries are producing the correct voltages.
I then installed the new capacitors and soldered the transformer leads directly to the bottom of the PCB to test.
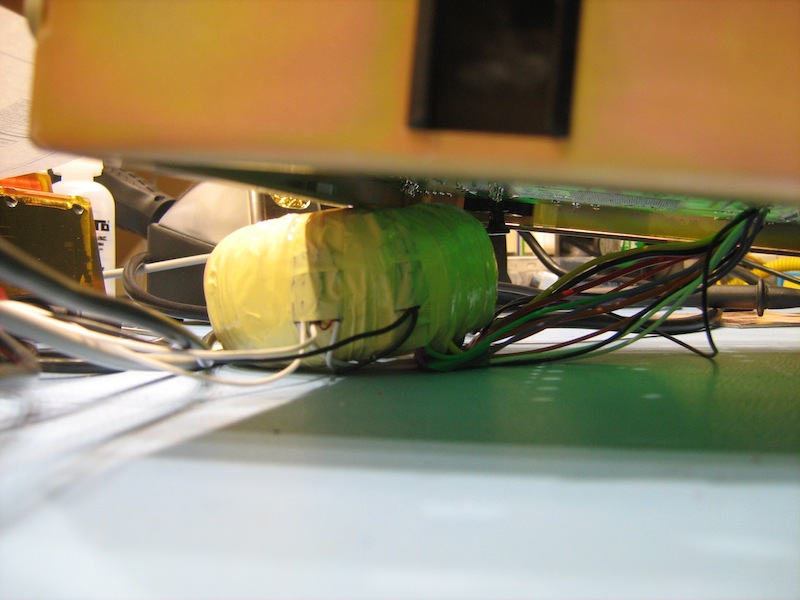
Looks good to me. Also a good opportunity to ensure that voltages on the various test points are within specification. Of course the allowable voltage tolerances on each of the test points is printed in the user manual.

OK cool, so it all works. However, the transformer needs to be mounted properly and I'm not even considering drilling or making any modifications to the original PCB.
I have taken two pieces of FR4 the same size. The upper one is for the new transformer to sit on and the bottom one will accommodate the pins and mounting bolt holes.
I have used M4 threaded stand offs for the screws that go through existing holes in the original main PCB to mount the whole assembly.
It's all constructed and ready to be encapsulated in thermally conductive epoxy.
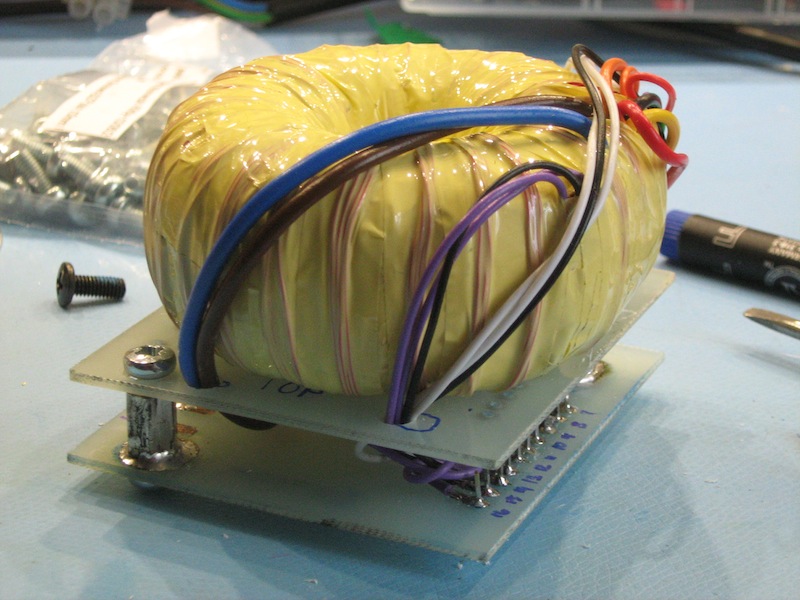
This is the mould. I have used polythene bags to act as a release agent. Most epoxy resins will not adhere to polythene.
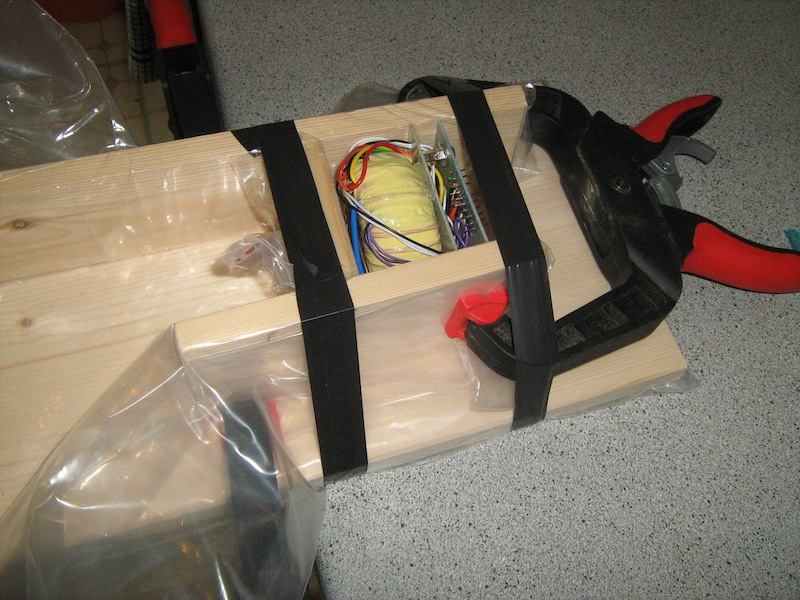
The epoxy is poured. Some is leaking out, but it's not a big deal. Also some wires have escaped encapsulation, but again, not a big deal.
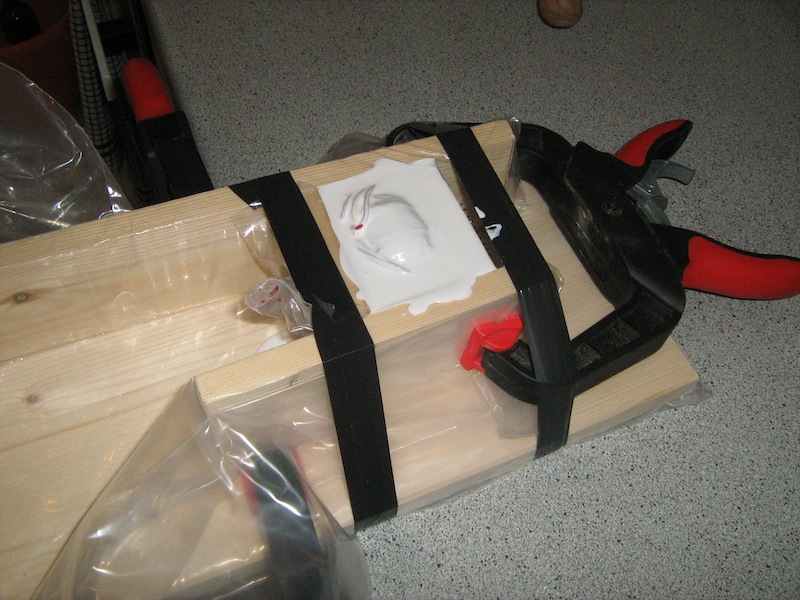
Whilst the epoxy set over the following 24 hours, I installed the new capacitors.
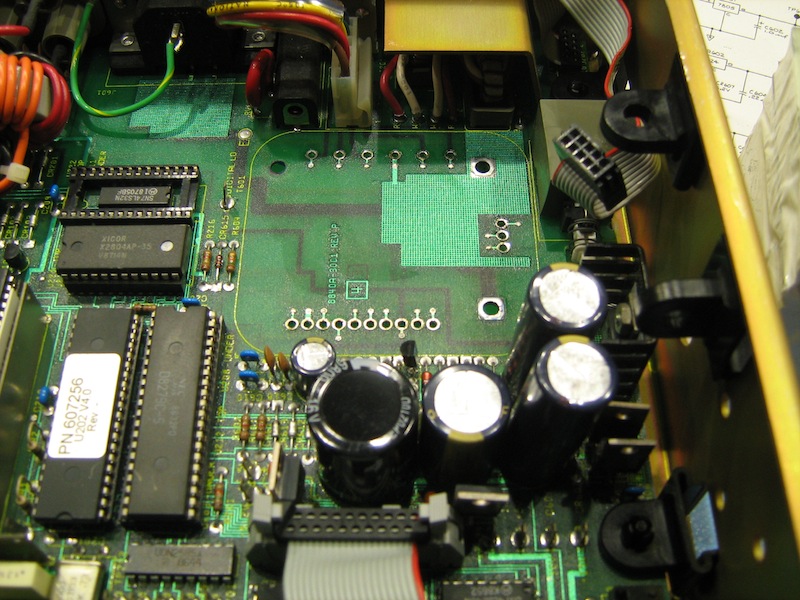
Finally, it's set and the mould released easily. It's a bit wrinkly from the polythene bags, no big deal. I didn't invest a great deal of time making sure the polythene was perfectly ironed out. Also the part of the transformer that is showing is because it was resting on the bottom of the mould.
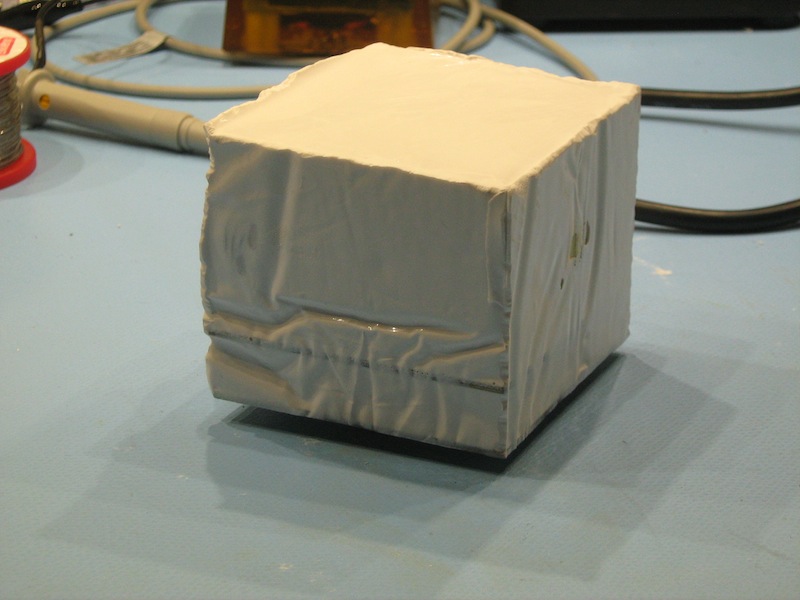
Then a bit of shaping with the Dremel so that the IEEE board would fit.
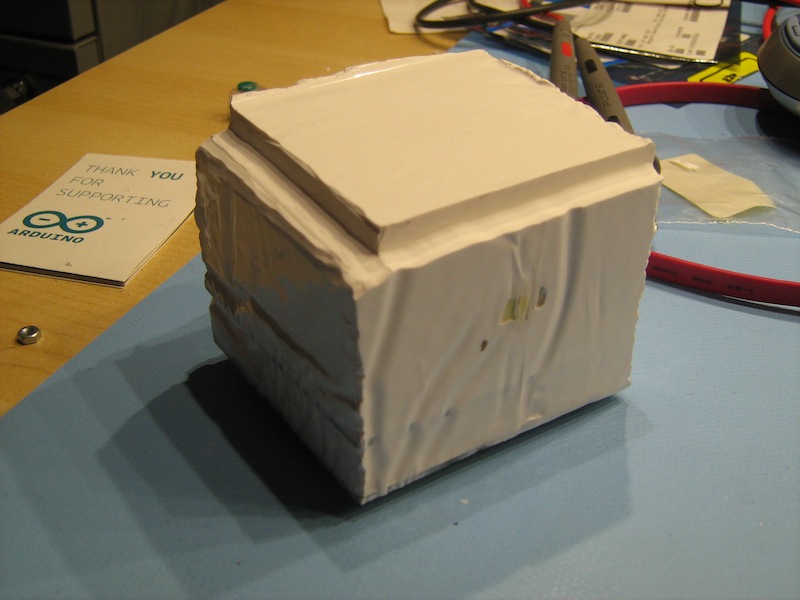
All of the bolt holes and pins lined up nicely. Although M4 screws were ever so slightly large for the holes in the main PCB, I didn't have to drill or modify any part of it. I guess the original holes were to accommodate some weird American size screws. Well, it is an American instrument after all, actually made in America - which is nice.
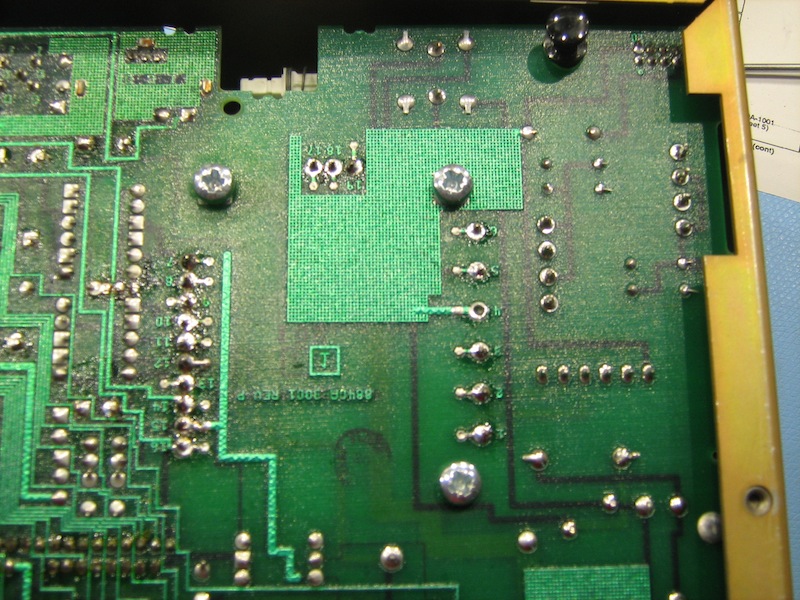
There it is all fully assembled...
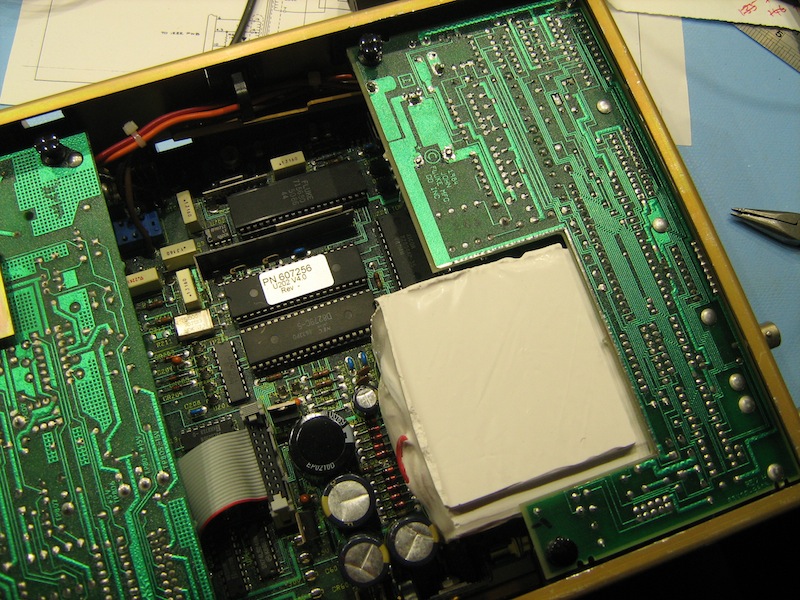
...and working. The VFD is much brighter too. It's AC feed comes from it's own pair of windings on the transformer, now that these are producing the correct voltage, the VFD works properly. Very impressed


I wouldn't be surprised to see another 30 odd years of service from this instrument.
Although I'm happy with the resolution and the insane input impedance, I'd very much like to have it calibrated. Although full calibration instructions are detailed in the user manual, I don't have a reliable or known reference, so I guess I'd better start saving.
