Here's an old Interpoint (now part of Crane Electronics) DC-DC module that I got for very cheap recently and opened up, for a look at power conversion in the aerospace world:


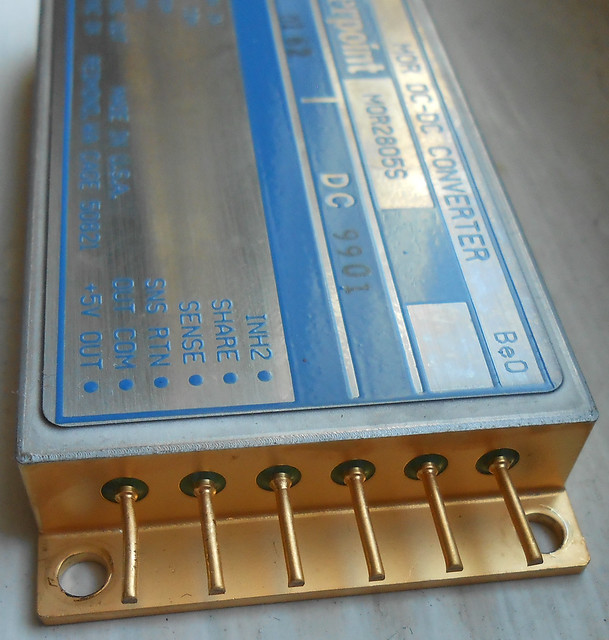
Sealed package with gold plating, hermetic feed-throughs, all the nice expensive stuff.
Once the lid is sawed off, very very carefully to not chip any ceramic substrates considering there's BeO inside, this is the inside:

The blue ceramic block is the control section, while the white ceramic at the top-left holds the input circuitry and the white ceramic at the right holds the output circuitry, with magnetics in the middle. The input and output ceramic substrates are likely the BeO, as it's used for its high thermal conductivity.
You can see that the input and output are isolated, from the way that the blue control section is split down the middle with a very clear gap. I'm not sure whether most of the control loop is on the input or output side, but it does have an interesting control-signal-isolation scheme with a small transformer (visible at the right side of the blue section), instead a normal optoisolator. I hear that optoisolators have a more severe lifetime limit, as the insulating material becomes more and more opaque over time, and the CTR eventually drops unusually low... It's possible this becomes a limiting factor in these type of applications, and that's why they're using a pulse transformer instead. There's lots of possibilities for sending a control signal through a transformer: you can amplitude- or frequency-modulate an oscillator, or do some PWM with simple square pulses. Analog Devices makes some digital isolators with tiny on-chip transformers and 100 Mhz+ frequencies.
Here's a closer look at the input...

...and the output...

...and the thin magnet wire from the current transformer (two secondaries, most likely?) that runs to both input- and output-side controls, probably for current-mode feedback on one side and over-current protection on the other side.

The connections to the pins (besides the power input and output) are done with a wide piece of flex circuit that wraps around the front and back, and solders down to the control board in various places:



Here's a high-level schematic, along with the corresponding parts:


The output might look a bit weird, but if you re-arrange some components while keeping it functionally equivalent, you end up with a standard forward converter:
Edit: replaced bad flash-heavy photos with better ones