I didn't check the datasheet for those leds, I just looked at the description on the page and noticed forward voltage = 3.2v and current = 150mA.
If you want to make everything compatible with 12v, the first chip (mic2287) is out. That chip is designed to use a low voltage (2.5-10v with an absolute maximum of 12v which won't work for you, because a 12v car battery may give you up to 14v and would damage the chip).
The chip would then boost the voltage as much as needed until the current going through the led(s) on the output reaches the amount you set. The idea would be to configure the chip to 150mA, you would set two leds with 3.2v in series on the output (so you'd have a 6.4v 150mA led) and then the chip would boost the 6v input voltage to 6.4v and light up the leds.
This chip only works in boost mode, so it's not easy to use such chip to light up just a couple of leds that don't need so much voltage.
The other two chips (bcr320/321) are however designed differently... you power the leds directly from the input voltage and after the leds you put this chip and the chip will only let a particular amount of current to the ground.
So with such chip, it doesn't matter if the input voltage is 6v or 12v (the chip supports up to 25v input voltage), you just put one or more leds in series and then after the leds you put this chip and configure it to only let 150mA (or whatever value you want) go through.
Naturally, with this chip, the input voltage must be higher than the voltage dropped on the leds and the chip itself ... so you can't use a 6v input voltage and put two leds in series (as these would need 6.4v to light up).
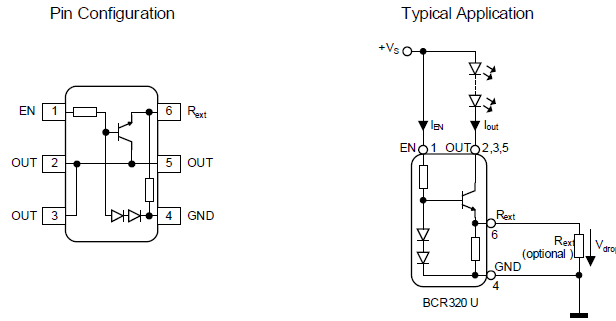
The led you linked has the leds connected in parallel , so you have a forward voltage of 3.2v and max current of 150mA ... so in the picture above you just have to have the input voltage higher than 3.2v and the resistor near the chip to about 5-6 ohm (which gives you 150mA):
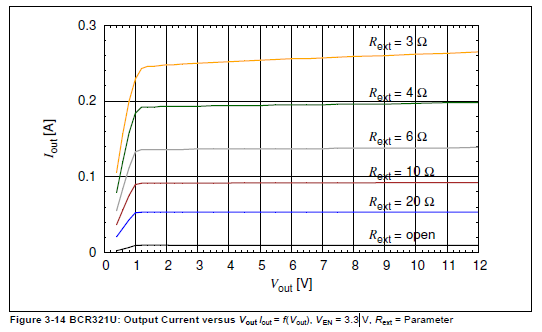
Note that there's some other gotchas you can deduct from the graphs in the datasheet, like the chip is only capable of 100mA when you give it at least 5v... but in your case, it's not an issue, you're gonna have at least 6 volts.
That's pretty much it... at least I think I got it right and I'm not writing something stupid.. it's 8 am here and I didn't sleep this night so I may be missing something obvious or making some mistake.