This switching power supply was built because I needed powerfull adjustable power supply for laboratory purposes. Linear topology would be unusable for this power (2400W - 2.4 kilowatts!). So I chose the switching topology of two switch forward (half controlled bridge). In my article about SMPSs it is a topology II.D. The switching upply uses IGBT transistors and is controlled by the UC3845 circuit. The schematic of my switching power supply you can see below. Mains voltage goes first through EMC filter. It is then rectified and filtered on capacitor C4. Due to high capacity, there's an inrush limiting circuit with Re1 switch and R2. Relay coil and fan (from PC power supply AT / ATX) are powered from 12V, which is obtained via resistor from 17V aux supply. Select R1 so that voltage at the relay coil and the fan was 12V. The auxiliary supply circuit uses TNY267. It is similar to described supply described here. R27 provides undervoltage protection of auxiliary power - will not turn on when less than 230V DC. UC3845 control circuit has the output frequency of 50kHz and a maximum 47% duty cycle. It is powered through the zener diode, which reduces the supply voltage of 5.6 V (ie to 11.4 V) and also shifts the UVLO thresholds of 7.9 V (lower) and 8.5 V (upper) to 13.5 V and 14.1 V. Source then begin work on power 14.1 V and never run below 13.5 V, which protects the IGBT from desaturation. The original thresholds of UC3845 were set too low. The circuit controls MOSFET T2, which drives gate drive transformer Tr2. It provides galvanic isolation and floating drive for upper IGBT. Via forming circuits with T3 and T4 it drives gates of IGBTs T5 and T6. They then switch rectified line voltage (325V) to power transformer Tr1. Its output is then rectified and finally averaged and smoothed by coil L1 and capacitors C17. Voltage feedback is connected from the output to pin 2 of IO1. The output voltage of the power supply can be set using the potentiometer P1. Galvanic isolation of the feedback is not necessary because the control circuit is connected to the secondary SMPS side and thus separated from the network. Current feedback is fed through the current transformer TR3 into 3 pin IO1. The threshold current of the overcurrent protection can be set by P2.
Transistors T5 and T6, diodes D5, D5 ', D6, D6', D7, D7 ', and the bridge should be placed on the heatsink. Diodes D7, capacitors C15 and protective RDC snubbers R22 + D8 + C14 should be placed as close as possible to the IGBT. LED 1 indicates operation of the supply, LED 2 indicates the current mode (overload / short circuit) or error. It lights up when the supply is not working in voltage mode. In voltage mode, on the IO1 pin 1 is 2.5 V, otherwise it is about 6V. LED lights can be omitted.
Inductance: Power transformer Tr1 I salvaged from an old powerfull 56V switched power supply. Transformation ratio of primary to secondary is about 3:2 to 4:3 and the ferrite core (EE shape) has no air gap. If you like to wind yourself, use a similar core as in the inverter So about 6.4 cm2 (acceptable range is 6-8 square cm). The primary is 20 turns of 20 wires, each has diameter of 0.5 to 0.6 mm. The secondary 14 turns of 28 wires together of the same diameter as primary. It is also possible to make windings of copper strips. On the contrary, the use of a single thick wire is not possible for reasons of skin effect (as it works with high frequencies). Halving the winding is not required, you can for example wind primary first and then secondary. Forward gate drive transformer Tr2 has three windings, 16 turns each. All winding are wound at once, by three twisted insulated bell wires. Is is wound on the ferrite core EI (EE may be) without air gap. I salvaged it from the main power transformer from a PC ATX or AT. The core has a cross section of about 80 to 120 mm2. Current transformer TR3 is 1 turn to 68 turn on the ferrite ring and the size or number of turns is not critical. In case of different number of turns you have to adjust R15. Auxiliary power transformer TR4 is wound on ferrite EE core with air gap and the cross section about 16 to 25 mm2. It comes from the auxiliary power transformer gutted from ATX. Orientation of winding of transformers (marked by dots) must be followed. Double choke EMI filter can be eg from microwave. Output coil L1 also comes from a 56V SMPS I gutted. It consists of two parallel inductors 54uH on the iron powder rings and the total inductance is therefore 27uH. Each coil is a wound by two magnet copper wires 1.7 mm diameter. The total cross section of L1 is then approximately 9 mm2.
L1 is connected to the negative branch, so the cathodes of diodes have no RF voltage and can be mounted on heat sink (or part of it) without insulation. Maximum input power of this switched power supply is about 2600W and efficiency at full load more than 90%. In this switching power supply I used IGBTs of type STGW30NC60W. They can be replaced by the types IRG4PC40W, IRG4PC50W, IRG4PC50U, STGW30NC60WD or similar enough powerful and fast. The output diodes can be any ultrafast with enough current rating. The upper diode (D5) sees 20A average current in the worst case, for the lower diode (D6) it 40A. The upper diode thus can be selected for half current than the bottom one. The upper diode can be eg two HFA25PB60 / DSEI30-06A or single DSEI60-06A / STTH6010W / HFA50PA60C. Bottom diode may be two DSEI60-06A / STTH6010W / HFA50PA60C or four HFA25PB60 / DSEI30-06A. Heatsink of diodes must dissipate a loss of approximately 60W. Loss of IGBTs can be up to 50W. The loss of D7 is difficult to predict because it depends on the properties of Tr1 (its inductance and coupling). Loss of the bridge is up to 25W. Source uses similar schematic as welding inverter since it works well. Switch S1 allows standby shutdown, because frequent mains switching of this powerful supply would not be appropriate (especially when used as laboratory power supply). Consumption in the standby state is only about 1W. S1 can be omitted. The supply is also possible to construct for a fixed voltage source. In this case it is advisable to optimize the transformation ratio of Tr1 for the best efficiency (eg, primary 20 turns and sedondary 1 turn for every 3.5 - 4V).
Attention!!! Switching supply is not for beginners, because most of its circuits are connected to mains. The mains voltage can occur on the output when improperly constructed! The capacitors can remain charged to dangerous voltage even after disconnected from mains. The output voltage can be above the safe touch voltage. This is the switchning power supply of high power. The AC input must have proper fuse, power outlet and the cable must be dimensed for the drawn current, otherwise there is a risk of fire. Everything you do, you do it on your own risk.
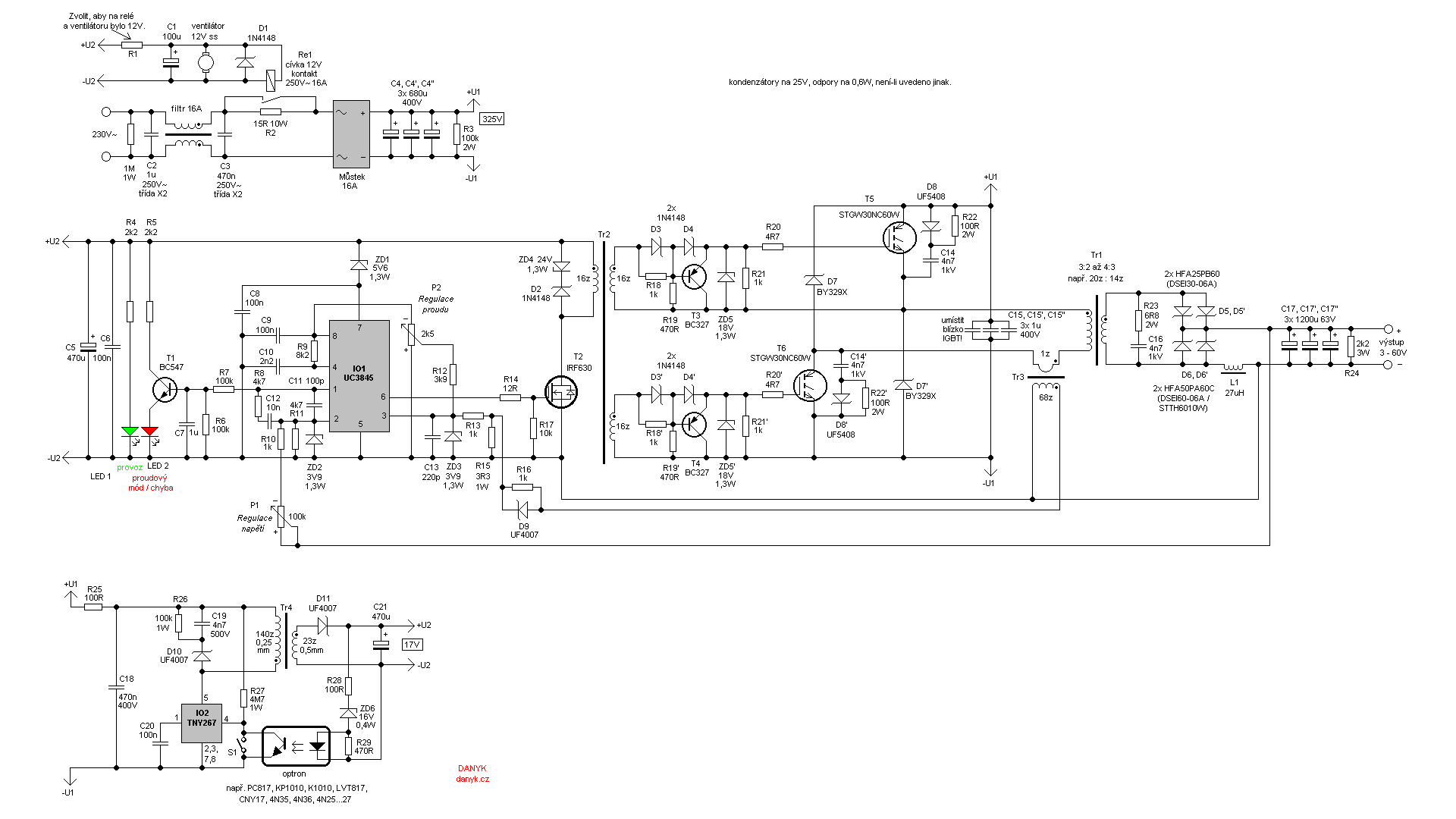
The schamatic of the high power adjustable switching power supply (SMPS) of 3-60V, 40A

Completed switching power supply

The front panel of the switching power supply - voltage control, current limit control, standby switch S1 and LEDs.
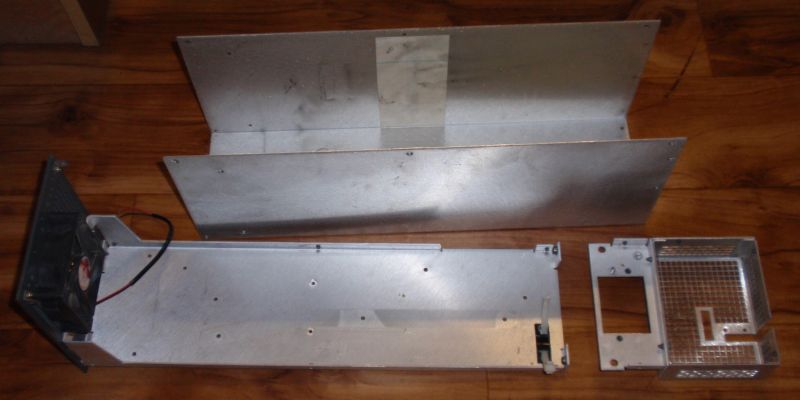
Box from the 56V supply ready for installation of my 3 - 60V supply

The original front panel

Box with 8cm fan.
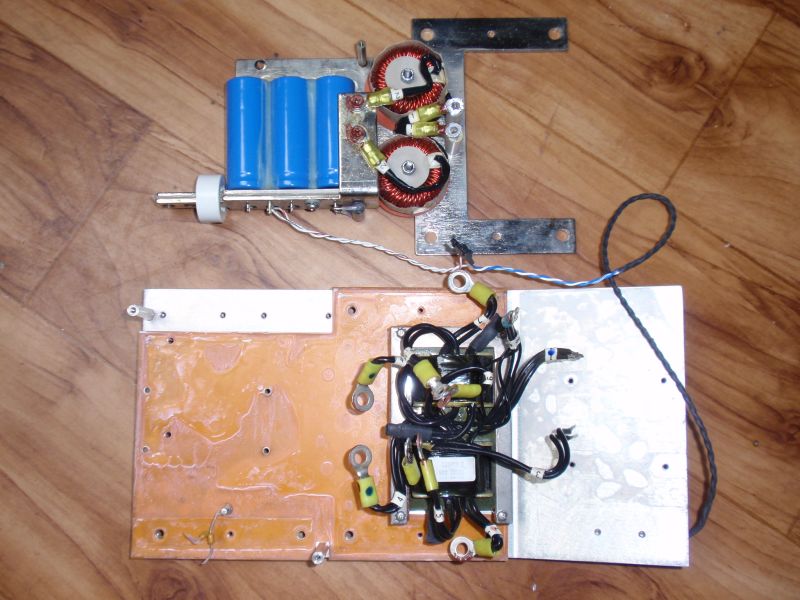
Heatsink, Tr1, L1 and C17 of the old power supply that will be used for construction of my supply.

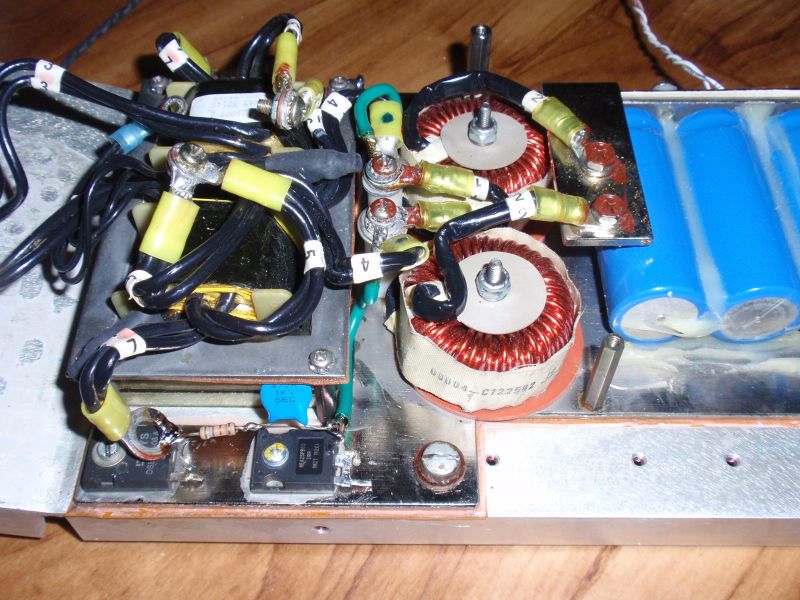
Prepared D5 and D6.

IGBT a reset diodes D7 on heatsink and the board prepared to be dremmeled.

Completed GDT (Gate drive transformer) Tr2.

The making of the board begins.

Completed power section, the control circuitry and the Tr2.
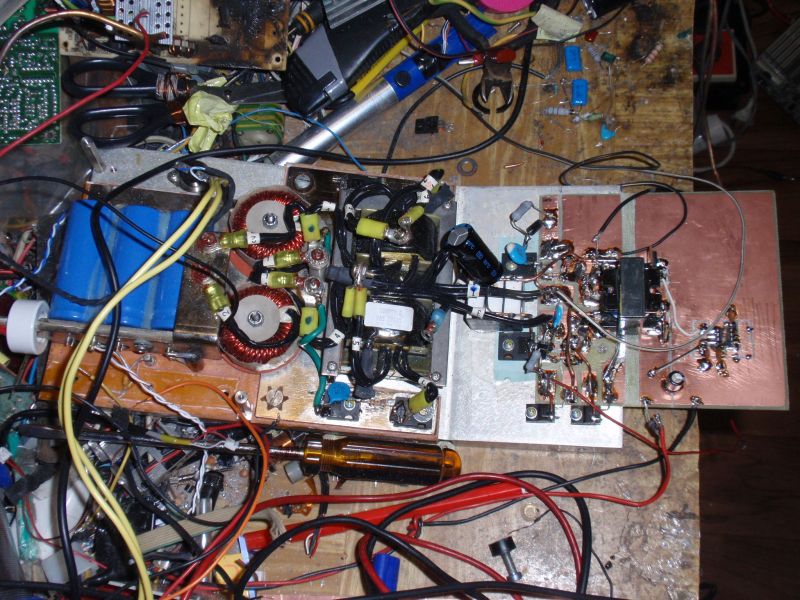
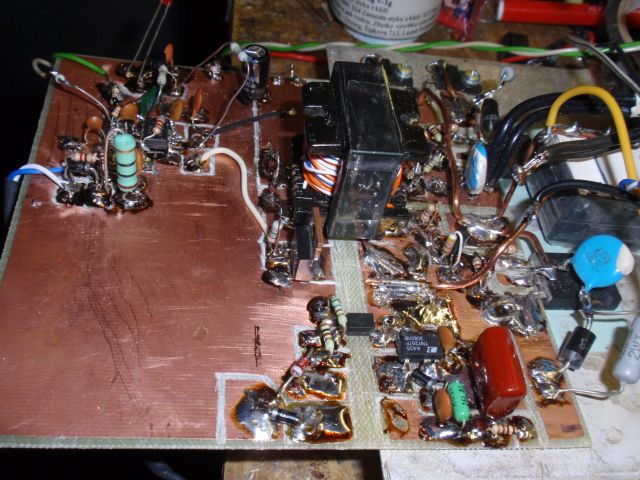
Building the auxiliary supply.
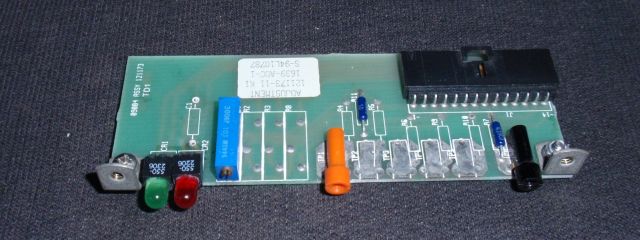
The board out of the old supply with LED 1 and LED 2.

Auxiliary supply afted the Tr4 soldered to it.

The switching power supply and the C4 capacitor (3x 680u)

Dummy load for testing of of the switching power supply: Spiral 230V 2000W from boiler adjusted to 57.5 V 2000W. I joined three branches, middle and both ends of the spiral are one outlet. The second outlet are tapped to the 1/4 and 3/4. This spiral is divided into 4 equal parts connected in parallel. The rated voltage is reduced the quarter, the resistance of the sixteenth and power is maintained.

The glowing spiral after connected to the tested switching power supply.

EMI filted and the inrush limiter.

Testing the switching power supply with the bottom of the box.

The inside of the completed supply.
For more information, I googled adjustable switching power supply and I found this article, which help me know more about the working principle of that sort of thing. Read it if you need:
http://www.apogeeweb.net/article/62.html